TECHNICAL SPECIFICATION
Creating a loudspeaker system involves a combination of design, technology and sensory considerations. Emotions communicated by listening to an audio system are the result of a complex process. Faital's Research and Development laboratory is a centre of excellence in the fields of research, planning, development, testing and support for the manufacture of loudspeaker systems. The Research and Development Department is entirely responsible for the planning and design of components using advanced CAD and FEA systems, as well as two-dimensional and complex-surface three-dimensional modelling.
The individual parts of each loudspeaker are directly designed in this way, in order to ensure that the end product will meet the Client's electro-acoustic and environmental requirements. Special attention is given to compliance of the finished product with environmental requirements and international standards.
1 • Co-Design
The major component of an audio system is the enjoyment that it transmits to the end user. This is the result of work that begins early on, once design models are ready. Initially customer's requirements are often not clearly defined. Therefore, Faital works in synergy with the customers right from the beginning. A number of meetings are required with the customer and the other suppliers involved in the project, in order to outline an initial concept of what the loudspeaker system will be like. A work group is set up within Faital, with representatives from all company departments, including design, sales, purchasing, quality, production and logistics. Based on their work, valuable suggestions will be proposed to the customer during the project, as well as strict quality control criteria at each stage of the project. Firstly the type, number and size of loudspeakers in the audio system need to be determined, as well as their position in relation to listeners sitting in the car, room, or relaxing in front of the television. The performance of the sound system will largely depend on this positioning, which is often the result of an optimisation based upon the customer design choices and needs.
2 • CAD System
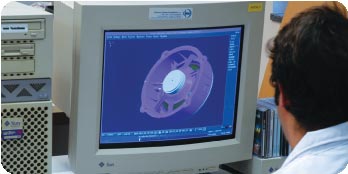
At this point, work can begin on drawing individual loudspeakers using three-dimensional modelling software, as well as their virtual mounting on corresponding assemblies.
In order to do this, both Faital and the customer must use the same software and be able to exchange files quickly containing the drawings.
Faital currently has 8 workstations and is able to carry out drawings using
four different CAD systems:
Autocad,
Computer Vision,
CATIA and
Unigraphics.
At the same time, an electro-acoustic simulation is carried out of the various loudspeakers in the system using "Finite Element Analysis" software techniques so that their acoustic performance can be predicted before they are built in the laboratory, based on the required physical and dimensional parameters.
The materials that will be used are also tested.
3 • Rapid Prototyping Techs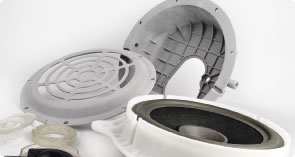
When the process of drawing and defining the technical characteristics of the various parts of the audio system has been sufficiently consolidated, Faital builds the first version of the loudspeakers. This stage is achieved by the construction of pilot tools or the use of rapid prototyping techniques, such as laser sintering of baskets, so that parts very similar to the final ones can be quickly put together. This allows electrical and acoustic measurements to be carried out in the laboratory, so that actual verifications can be made as to the compliance of products in relation to project specifications. At this stage the working group assigned to the project, co-ordinated by the project leader, can predict reliability problems in the final product using third-generation
DFMEA methods. In addition, aspects relating to the industrial manufacturing of individual parts can be assessed, providing an initial outline of production flow and defining any special manufacturing equipment that will be required. This verification stage is extremely important. In addition to allowing the required adjustments and changes to be made to the loudspeakers, this stage provides an opportunity to present useful suggestions to the customer for
improving overall the product,
including audio amplifiers or DSP that may influence the quality of the audio system.
All problems that are found and any changes that need to be made to individual parts are discussed at appropriate inter-functional progress meetings. This allows their possible impact both in terms of cost and production, to be assessed using a detailed reliability evaluation based on advanced
PFMEAs, while ensuring that development deadlines are maintained. Obviously, the customer is involved in this stage so that any changes to the initial technical requirements can be agreed upon.
4 • Off-Tool Parts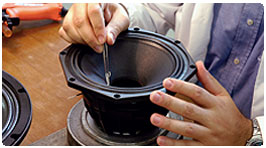
Once this stage has been completed, work can start on the production of final tools and equipment for the manufacture of all parts. Attention is now focused on
second-level suppliers and production methods: purchasing, quality of suppliers and production methods, play an important role in this stage. At the proposed production plant an initial review of the manufacturing process for the loudspeaker being developed is carried out. This allows control plans and production flow process to be optimised by clearly identifying process variables. On receiving final of tool parts and equipment, the supplier quality department and the laboratory carry out a key role once again. While the laboratory undertakes manual assembly of all loudspeakers required for the audio system in order to verify their compliance with project specifications, the quality department "certifies" the quality of supplies. This is carried out using the pre-series products in accordance with similar criteria as to that required by the end customer. This process continues even after mass production start up and is based on a continuous performance-monitoring plan.
5 • Acoustic Testing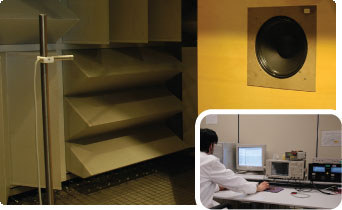
In addition to
instrumental testing, the samples produced in the laboratory are subsequently used for a series of tests, in co-operation with the customer, these tests range from installation testing to dimensional compatibility, as well as verifying the system's acoustic performance. Final adjustments of acoustic performance, which will be experienced and assessed directly by the end user, can still be made by
fine tuning and implementing minor changes in this way the final characteristics of the manufactured product can be set.
Sound is evaluated by tests using instruments and through a series of listening sessions carried out by specially trained engineers. Carefully selected pieces of music are used in order to highlight specific features of the audio system's acoustic performance.
The listening tests are also compared with audio recordings that have been made in a reference environment, such as a specially equipped listening room.
6 • Pre-serie Production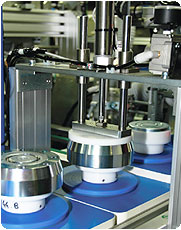
When the results that have been achieved are considered satisfactory, a pre-series production is undertaken in the plant. This allows verification that the products manufactured in the final production process comply with
project specifications, as well as the various supply specifications required by the customer.
Pre-series production, which is carried out using the final manufacturing equipment on the proposed production line, marks the beginning of
product and process validation both aspects are subject to careful quality control.
This allows the plant committee, supported by engineers from the
Research & Development laboratory, to carry out an initial review of the effectiveness of the production processes that had been previously planned. At this stage a verification is carried out to ensure that process variables are under control, based on accurate measurements and using appropriate statistical methods.
Any deviations or problems that are found generate immediate feedback regarding the project, in addition to the necessary corrective action being taken in relation to the product, processes and suppliers.
7 • Validation testing 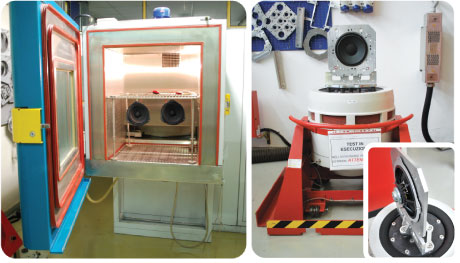
The loudspeakers from the pre-series production are then used for all validation testing,
which is carried out at Faital's laboratory based on the customers specifications. The tests used to verify the reliability and performance of loudspeakers during their lifecycle vary enormously from customer to customer. As Faital has acquired a very wide experience in this area, it is able to share its know-how with customer by suggesting the most appropriate solutions and methods. Faital has for sometime implemented a series of routine activities to be applied during this phase of product development and manufacture. These activities include salt fog tests, life tests, temperature and vibration test either carried out singly or combined together, as well as electric-acoustic asserments.
All these activities result in a detailed document that completes the validation stage of the loudspeaker system. The project review meetings that are held by the
quality department and laboratory allow any problems to be monitored and corrected.
8 • Production 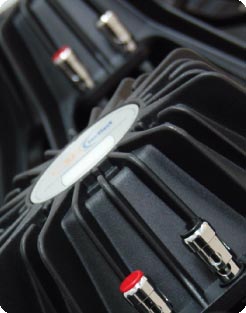
The project has been completed. From this point, the production department is responsible for ensuring that production volumes required by the customer are met and verified using
R@R (Run @ Rate) tests, in accordance with product characteristics set out in the project specifications.
Production processes are verified and optimised through continuous quality control on the production line. All loudspeakers manufactured by the Faital group are fully checked when they come off the assembly line. Loudspeakers are tested individually using special computerised equipment, which verifies in real time six electro-acoustic parameters relating to nominal use conditions specific to each product. Defective items are rejected.
Quality Assurance and the Plant Committee continuously monitor production progress. In the case of non-conformities or a deterioration in the level of production rejects corrective actions, either internal or relating to second-level suppliers, are identified and implemented. In addition, a general management committee oversees the progress of all Faital plants throughout the world, in order to ensure that a uniform level of product quality is achieved wherever the customer requires manufacturing to be carried out.
Manufactured products are provided with a
Free Pass and tracking codes are sent to the warehouse. Finished products are shipped in accordance with the customers delivery schedules, received via
EDI (Electronic Data Interchange). Products are labelled and packaged as previously agreed with the customer.
Most of a product is emotion and Faital ensures the emotion of perfect sound.